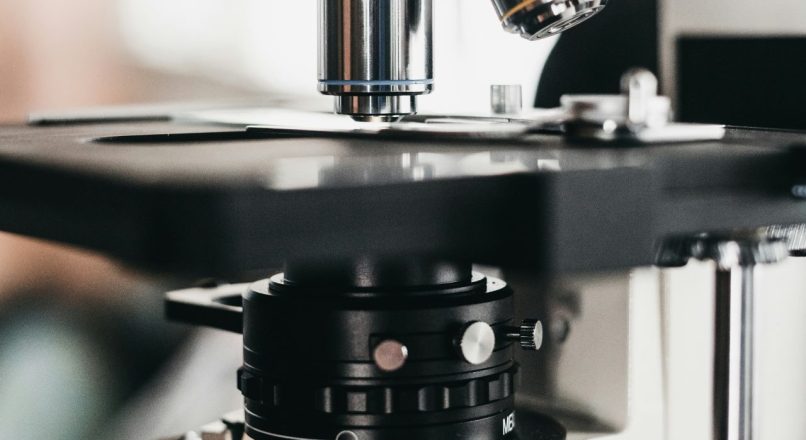
AtoAtomic Force Microscopy (AFM): Essential Parts and Their Functions Explained
Principle of AFM
Atomic Force Microscopy uses a nanometer‑scale cantilever tip to map surface topography with sub‑angstrom vertical resolution. The 2025 Global AFM Market Report estimates that over 12,000 instruments are currently in service worldwide, a 6.4 % CAGR since 2020.
Core Components
Component | Function | Typical Spec |
---|---|---|
Cantilever & Tip | Interacts with sample via van der Waals forces; deflection encodes height. | Spring constant 0.02–40 N/m |
Laser Diode | Reflects off cantilever backside to position‑sensitive detector. | 650 nm, <1 mW |
Photodiode Detector | Measures beam deflection with <0.5 nm noise floor. | Quad‑segment Si photodiode |
Piezoelectric Scanner | Moves sample or tip in x‑y‑z with atomic precision. | Range 100 µm × 100 µm × 15 µm |
Feedback Controller | Maintains constant force by adjusting z‑position at >10 kHz bandwidth. | PID digital loop |
Operating Modes
- Contact Mode: Continuous tip‑sample contact; high lateral resolution but risk of damage.
- Tapping Mode: Cantilever oscillates near resonance; reduces shear forces by ~90 %.
- Non‑contact Mode: Tip hovers in attractive regime; ideal for soft polymers and biological samples.
Performance Statistics
State‑of‑the‑art AFMs achieve vertical noise < 50 pm RMS and lateral resolution better than 1 nm. In a 2024 inter‑laboratory comparison (NanoScale Metrology Consortium), the mean roughness (Ra) measured on a silicon calibration grating differed by only 1.8 % across 25 facilities.
Maintenance Checklist
- Replace laser every 5 000 operating hours to avoid 15 % signal loss.
- Calibrate piezo scanner monthly; drift >2 % can skew height data.
- Store cantilevers in a desiccator to prevent Q‑factor drop from humidity.
Conclusion
A clear understanding of each AFM part enables researchers to push imaging limits while protecting delicate samples and expensive hardware.
References
- Global AFM Market Report, Allied Analytics, 2025.
- NanoScale Metrology Consortium. “Round‑Robin AFM Roughness Study,” 2024.
Leave a reply